Europe must take decisive steps to simplify and modernise its rail systems to strengthen competitiveness,...
Novel electric propulsion systems for trains, trams, and metros offer an opportunity to reduce energy consumption, weight, volume, and maintenance costs.
The Challenge
The electronic technology currently used in traction drives is based on silicon (Si) materials, which face some significant limitations. High losses, frequent failures and requires large, often heavy equipment.
How we do this?
Silicon Carbide (SiC) is emerging as a new alternative to Si materials. Enabling high-speed switching and lower losses, SiC-based devices are being investigated for their ability to optimise traction systems.
With the goal of paving the way towards more efficient traction system architectures, the Traction System Technical Demonstrator (TD) developed 5 SiC-based demonstrators.
• Dual system tramway AC traction system
• Metro traction system
• Suburban rail AC traction system
• Regional train full traction sub-system
• High-speed train (HST) traction system integrated in train based on independent rotating wheels
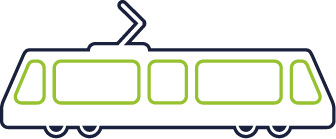
Dual system tramway AC traction system
How a SiC metal-oxide-semiconductor field-effect transistor (MOSFET) affects an AC traction system used for dual system tramways, with a specific focus on how it impacts energy consumption, weight, and volume.

Key finding
How a SiC metal-oxide-semiconductor field-effect transistor (MOSFET) affects an AC traction system used for dual system tramways, with a specific focus on how it impacts energy consumption, weight, and volume.
Conclusion
SiC MOSFETs have the potential to improve traction systems.
Who benefits
Railway operators and
Suppliers
TRL reached
TRL 5 (technology validated in relevant environment).
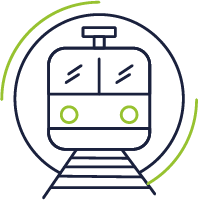
Metro traction system
1. How the use of SiC-based technology can reduce volume, weight, and maintenance costs while also increasing energy savings and reliability.
2. The benefits of using SiC devices in other stages of the powertrain, including the DC/DC and input AC stages.

Key finding
Results obtained were better than expected, with an improvement of approximately 4% (expected improvement was 2.43%).
Conclusion
Using SiC technology offers significant opportunities to improve efficiency at different stages of the traction system.
Who benefits
Railway operators and
Suppliers
TRL reached
TRL 7 (system prototype demonstration in operational environment).

Suburban rail AC traction system
Optimising the main transformer, as well as the traction motor, as a means of minimising energy losses and reducing the motor’s weight.

Key finding
The optimised system’s total losses, including SiC-based traction inverters, was 24% lower than the base system.
Conclusion
The prototype AC traction system for suburban applications addresses key customer requirements, including reducing maintenance, energy and overall costs; decreasing volume, weight and noise; and increasing reliability.
Who benefits
Railway operators and
Suppliers
TRL reached
TRL 3 (experimental proof of concept).

Regional train full traction sub-system
A prototype consisting of newly developed components covering the full traction SiC sub-system – from the pantograph to the wheels – for an AC catenary voltage.

Key finding
Energy consumption measurements confirmed the theoretical energy saving of 13% (train), with energy savings on a regional route profile being 12.8%.
Conclusion
The new full traction sub-system based on SiC high-power density converters, high efficiency transformer and high-speed motors and gear box can improve the performance of the entire traction system.
Who benefits
Railway operators and
Suppliers
TRL reached
TRL 7 (system prototype demonstration in operational environment).
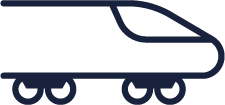
High-speed train (HST) traction system integrated in train based on independent rotating wheels
Evaluated a 350 kW motor on wheel solution designed for direct drive configuration with high efficiency.

Key finding
The motor on wheel solution provided up to 60% of the maximum brake required in emergency, reaching 2.6 kNm during 100 seconds per wheel without sustaining any damage.
Conclusion
While the motor’s measured efficiency is lower than expected, it nonetheless achieves the desired speed/torque performance – positioning it as a potential solution for achieving improved traction system performance at the train level.
Who benefits
Railway operators and
Suppliers
TRL reached
TRL 6 (technology demonstrated in relevant environment).
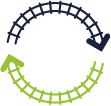
Paving the way to more efficient traction systems
By developing new, SiC-based traction components and subsystems, the TD successfully paved the way towards more efficient traction system architectures, including for use in metro, regional, and high-speed trains.