Important Update: Deadline for Women In Rail 2025 Awards Extended Great news for all those eager to make their mark in...
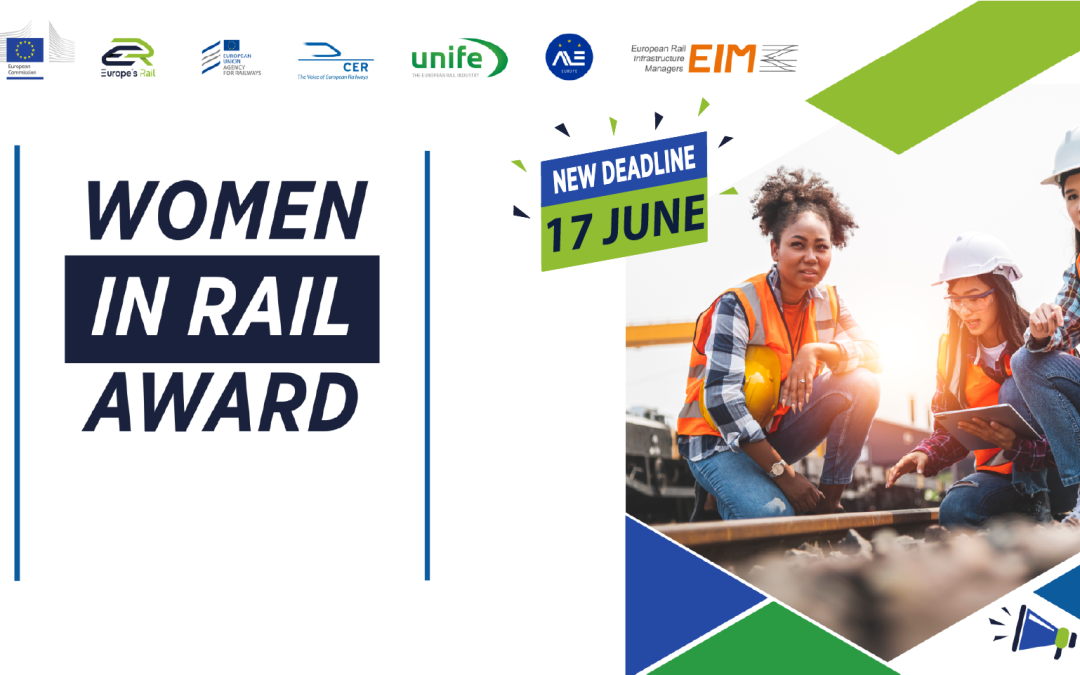
Keeping trains, track and infrastructure in tip-top condition
Maintenance is key to ensuring that European railways remain safe, reliable and efficient. However, the costs of maintaining and renewing the continent’s rail infrastructure each year come to more than €25 billion and they are forecast to rise steeply in line with the expanding rail networks and demands for services.
Historically, much of the maintenance on railways in Europe has been carried out manually and at fixed intervals. This can result in long disruptions to rail service, frustrating both the rail operators and passengers. However, new technologies and especially data analytics bring hope of improving this situation. These can enhance the ability of operators to assess the condition of key rail assets, thus optimising decision-making on the need for and urgency of maintenance. Data-driven technologies – including those associated with Intelligent Asset Management – are set to foster better asset management on railways. This in turn will help to boost the efficiency and attractiveness of railways, while reducing overall costs for their operators and users.
Under EU-Rail, building on the work of its predecessor programme Shift2Rail, new innovations were demonstrated for integrating autonomous systems/machines and worker’ physical support (exoskeleton) in railway maintenance, including their Cost-Benefit Analysis and assessments against Key Performance Indicators (KPIs).
Demo: On-Track Autonomous Multipurpose Mobile Manipulator (OTA3M)
Discussion
The goal was to achieve accurate control of the OTA3M, a robotic version of a human-operated on-track machine (OTM), which can manipulate heavy rail infrastructure components and materials, and has a reach of several metres. Researchers focused on the way that hydraulic road-rail excavators behave and move, and they also ensured the system’s efficiency and safety in autonomous operation. This involved developing: trajectory scaling algorithms to manage the machine’s movement; a fast-reacting network of Inertial Measurement Units (IMUs) for accurate sensing and control; plus an autonomous running mode with safety features, e.g. a wireless emergency stop system and an outdoor-certified safety laser scanner. The developed prototypes have been tested on a modern excavator.
Key findings
Demonstrations, which included autonomous ballast cleaning, showcased the effectiveness of the OTA3M’s trajectory scaling algorithm and the IMU network. There was notably a 92% reduction of exceeding the working gauge. The autonomous control functionalities significantly improved the performance and efficiency of road-rail excavators.
Several innovations were demonstrated: (i) enhanced control accuracy and reduced tracking errors, thanks to the pump flow-limited trajectory scaling algorithm; (ii) improved real-time sensing and control through the developed IMU network, and thus more precise excavator arm movements; (iii) increased safety and operational efficiency, thanks to autonomous running modes and safety systems; and (iv) fewer trajectory deviations and enhanced task execution speeds without exceeding pump capacities.
The detailed results and demonstrations highlight the project’s potential to enhance autonomous excavator operations, promising significant advancements in efficiency, safety, and control accuracy.
Optimised operational procedures resulted in a 20% reduction in task operation time; and a positive Economic Net Present Value (ENPV) of €90 million over 20 years, including an Economic Rate of Return (ERR) of 54.3%.
Next steps
Further refinement of the prototypes and more extensive field tests, to convince EU rail companies to take this autonomous excavator.
Demo: Occupational Back-support Exoskeleton (oBSE)
Discussion
Researchers developed the Occupational Back-support Exoskeleton (oBSE), a prototype fitted with various sensors and IoT (Internet of Things) capabilities. This exoskeleton is designed to assist workers in lifting and carrying tasks, by reducing the physical strain on their bodies.
Key findings
The exoskeleton developed was demonstrated in real-world scenarios, showing its effectiveness in reducing muscular fatigue during heavy lifting tasks. Musculoskeletal loading was reduced by up to 50% and there was an improvement of worker productivity and safety.
Next steps
Further research and innovation (R&I) to explore opportunities and potential commercial applications for this new exoskeleton for rail workers.
Demos: Unmanned Ground Vehicle (UGV) and End Effector
Discussion
The main goal was to enhance railway maintenance efficiency, by developing and demonstrating unmanned ground vehicles and end effectors controlled via a command and control system. Researchers developed and demonstrated two prototypes:, an Unmanned Ground Vehicle (UGV), an autonomous vehicle equipped with a command and control system for inspection and maintenance tasks; and an End Effector, a robotic device designed to screw and unscrew rail fasteners, improving production speed and reducing manual labour.
Key findings
The UGV demo, conducted at Northampton and Lamport Railway in the UK, showcased obstacle detection, navigation, and defect inspection capabilities. The End Effector demo highlighted effective handling of rail fasteners, achieving the targeted production rate in controlled environments. Both prototypes reached TRL 6/7, indicating successful operational demonstration in relevant environments, and aligned with industry standards to ensure they met necessary safety and operational guidelines.
UGV: improved obstacle detection accuracy and enhanced cycle times for maintenance tasks, averaging around four minutes per cycle.
End Effector: reduced ergonomic risks for gross positioning tasks; also increased production capacity to 302.5 sleepers per hour, surpassing the target of 300.
Next steps
Future work should focus on refining prototypes for broader adoption in the industry. More generally, EU-Rail will exploit the outcome of this demonstrator in FA3 with the development of a modular and open-source robotic platform.
Keeping track of railway assets, from trains to track and all associated infrastructure, plays an essential role in improving the overall rail system. Supported by digitalisation, Intelligent Asset Management is gaining traction as a means to manage, monitor, maintain and optimise these rail assets.
Under Europe’s Shift2Rail Joint Undertaking, a predecessor of Europe’s Rail, an Intelligent Asset Management System (IAMS) was successfully demonstrated through more than a dozen different Work Package deliverables. The results of these deliverables were combined within an Integrated Technology Demonstrator. This ITD aimed to collect both data (Railway Integrated Measuring and Monitoring System, RIMMS) and extract knowledge (Dynamic Railway Information Management System, DRIMS), in order to develop maintenance strategies to support human decisions using IAMS.
Core components of IAMS
DRIMS: focused on interfaces with external systems; maintenance-related data management and data mining and data analytics; asset degradation modelling, covering i) degradation modelling driven by data and ii) domain knowledge and the enhancement of existing models using data/new insights.
RIMMS: focused on asset status data collection (measuring and monitoring) plus processing and data aggregation producing data and/or information on the measured/monitored status of assets.
IAMS: focused on decision-making (based on DRIMS, etc.); validation and implementation of degradation models based on combining traditional and data-driven degradation models and embedding them in the operational maintenance process based upon domain knowledge; system modelling; strategies and human decision support.
Demo: Italian Urban Metro System IAMS
Discussion
Milan’s public transportation (Metro, bus and tram service) is operated and maintained by ATM. It faces two challenges: optimising and automating its current maintenance strategy; and automatically suggesting one or more best alternative services when operations are limited. The company aimed to solve the first challenge through a context-driven Human-Machine Interface (HMI). Besides highlighting anomalies, this can enable the maintenance manager and operators to visualise/predict the status of current assets. Challenge two can potentially be solved by using real data, e.g. asset state information, weather data or passenger flows.
ATM and Hitachi Rail STS defined, deployed and tested a IAMS TRL 6-7 demonstrator, with the goal of improving the current maintenance on Metro Line 5. These were the three types of assets selected: track circuits, track maintenance and wheel defects, and on-board signalling.
Key findings
In an operational Metro environment such Metro Milan Line 5, the IAMS tools helps to detect anomalies, increases the availability of data for operators and can reduce service disruption, which in turn reduces financial losses.
Specific results:
Demo: Digital Twin for Railway Asset Management: Application to the French and Spanish Railway Network
Discussion
Digital twins are computer programs, calling on real-world data to digitally represent and thus predict how a system will perform. They are increasingly used in rail system operational and maintenance performance. In this deliverable, researchers created digital twins of new track sections and a new catenary system section of the railway infrastructure, for the French and Spanish rail networks. Processes were also developed to register and digitalise the evolution of these networks, the ‘As Built Records’ (ABR). These updates are useful to optimise maintenance, e.g. inspection, railway operation, monitoring purposes and intelligent asset management strategies.
The main objective of this Digital Twin was to provide services to the asset managers for better, faster, more efficient maintenance. Extensive field work and interviews were conducted, to discover which information, data, assets and activities should be demonstrated in the Digital Twin, if the solution is to be accepted by business users.
Work focused on demonstrating three main functions:
Key findings
A Digital Twin of rail assets was developed and successfully operated. It comprised the latest updates to a 3D database of the assets (i.e. the digital twin) and the results of operations of the software module developed (merging and data structuring, automatic patterns and object recognition, new maintenance planning and asset degradation prediction).
The Digital Twin can be integrated into a rail operator’s existing information system, as a service providing a complete and powerful solution to asset managers. It is also a scalable solution, easy to maintain, easily integrated with databases, compatible with clouds and other applications, and a good solution to meet the real requirements of asset management on railways.
LIDAR technology is well suited for the work surveys done for the renewal of track and catenary components. Terrestrial LIDAR acquisitions can be complemented by drone acquisitions, for high-definition imaging.
For the maintenance planning assistance part, the AVATAR prototype has been deployed in 10 maintenance business units in France. The satisfaction of prototype users is 81% after 4 months of use.
Next steps
The industrial deployment of the application started in January 2023, with a target of 1,500 users on the whole French railways network.
Demo: Anomaly Detection for Rail Fastener Systems
Discussion
Rail fastening systems are a key component in a railway track system, fixing the rail to the sleepers. If fasteners fail, this can affect the track or trains and at worst even lead to accidents. Track inspections are therefore essential, but can be time-consuming or inaccurate if done manually by maintenance teams. One solution is to inspect the track with automated visual inspection or eddy current sensors (electromagnetism), like the Lindometer. This was invented to tackle deficiencies in existing rail fastener anomaly detection systems (based on CCD, video or laser technologies), due to the harsh environment encountered in the north of Sweden.
A new prototype of the Lindometer, featuring updated version hardware and rail fastener analytics, was developed. Tested along 2.5 km of the iron-ore line in the north of Sweden, the device was mounted on an unloaded freight train 110mm above the rail head, with the train moving at 70 km/h
Key findings
The prototype Lindometer was able to detect fastener signatures from 110 mm above the railhead, during the validation test. Thanks to the advanced new anomaly detection technique, it was able to detect all the anomalous points precisely and to separate them from the healthy group of points from the measurements recorded from an in-service train. The new rail fastener anomaly detection system is suitable for a rugged and reliable detection system and can be used in adverse weather conditions.
Demo: Remote Condition Monitoring Maintenance Reduction Interventions and Decisions: In Field Validation
Discussion
Alarms related to false assets are a problem for rail maintenance managers, who must deal with many different alarms in their job. Researchers therefore carried out an investigation in partnership with Network Rail in the UK, assessing the main and most frequent causes of alarms, and how their criticality relates to the frequency of a maintenance activity. The study tested two new algorithms against various data, in order to improve the efficiency of asset-related alarms for maintenance, focusing on track circuit low clear alarms and point swing anomaly alarms.
Workshops were also organised, to gather information about the most frequent alarms that maintenance managers face. There were also discussions on the practicality of including automated systems for these algorithms in the Infrastructure Asset Management Systems.
Key findings
The demo proved successful when used to detect point alarms and this algorithm is now being offered as an additional feature in TIRIS, an asset management system for predictive maintenance. So the algorithm has gone beyond the prototype stage and is today fully supported as a legitimate feature available to infrastructure managers to call on in real systems. The added level of information on anomalous point behaviour provides ample opportunity to optimise maintenance scheduling and ultimately reduce maintenance costs.
For track circuit alarms, the precipitation compensation algorithm has proved less reliable and needs more testing and fine-tuning.
Next steps
The algorithm for points anomaly detection and classification could be improved, e.g. looking at the impact of changing seasons and weather conditions on assets behaviour. The track circuits algorithm could be enhanced by focusing on automatically detecting which assets are affected by the rain.
Demo: SMART maintenance on rail freight corridor Rhine-Alpine
Discussion
SMART maintenance calls for predicting the condition of rail track geometry, to increase the proportion of predictive maintenance and thus reduce the proportion of reactive maintenance. A further goal is detecting anomalies in the track geometry, track construction and rail surface: this can provide information about the root causes and eliminate them when possible. Models to predict the deterioration of track geometry and to detect anomalies are partly available on the market, but are usually not suitable for working under real conditions.
For this deliverable, researchers developed a digital representation of selected track sections of the Rhine-Alpine rail freight corridor. This representation includes technical information about the asset as well as the historical and actual condition, plus models to detect and classify anomalies, and to recognise patterns or degradation of the assets.
The aim of this deliverable was to plan and implement necessary maintenance activities on the selected sections of the corridor and to provide real data for the final evaluation. Besides the planning of maintenance activities, another objective was to improve and implement ‘lean tamping’, i.e. to measure tracks using operational trains at high speed and with great precision, rather than calling on pre-measurements made by people on the tracks. The data gathered was used by tamping machines that correct the track shape.
Key findings
All developed models performed very well, detecting anomalies in combination with root cause analyses and providing a prediction model for the deterioration of track geometry. The results are an important input for a smart planning process. In particular, the degradation model gave exceptionally good results with high accuracy. The detection of anomalies in the rail surface and track design showed a hit rate of over 95%, but the classification still needs to be improved to avoid manual interventions.
On the execution side, the lean tamping process developed and tested here was further developed to increase the benefits of this process. A new tamping procedure, which gathers additional data during tamping of track geometry, was also evaluated.
Taking into account anomalies, root causes, and predictions, a much more efficient maintenance planning and execution is possible. Lean and combined maintenance execution increase sustainability and quality of the maintenance activities and the capacity of the track.
Next steps
Follow-up research in Europe’s Rail will aim to build on these results and increase the TRL level, as well as to improve the maintenance planning and scheduling on the rail freight corridor between Rotterdam and Genoa.
Demo: Integrated Asset Management for Civils – Track
Discussion
This demo was run by Network Rail in the UK, and involved an OTM DST (On-Track Machine Decision-Support Tool) that includes the analytics to support the planning of maintenance activities on the track. The tool can predict track degradation over the next year or so, determine when an intervention is required, and recommend the type of intervention (e.g. tamping or stone-blowing). The demo’s detailed screen allows a user to enter the required route and track geometry data. Results were measured and validated by linking the Key Performance Indicators (KPIs) under maintenance and planning delivery, asset life, train service impact (due to track condition), safety risk and environmental impact.
Key findings
The developed tool can inform end-users (e.g. a Route Access Manager or Track Maintenance Engineer) when to schedule the next track maintenance and the most appropriate type of intervention. This enables managers to devise a prioritised maintenance plan for track geometry on plain lines, but not on switches and crossings.
The demo was tested in a typical operational environment by potential end-users using real-world scenarios. User feedback suggested the demo achieved the requirements of TRL 6 to 7; it could even reach TRL 8, if the tool was used in existing systems.
Demo: Integrated Asset Management for Civils – Bridges
Discussion
The aim of the Life Cycle Engineering (LCE) for Bridges demonstrator was to provide a decision support tool, which can be used to optimise maintenance and replacement planning (by considering the overall costs) for the existing bridges at Wiener Linien, the company that runs most of the public transit network in Vienna, Austria. By comparing and considering different maintenance strategies, a user can evaluate what is the best technical solution for a given, limited budget.
Key findings
The LCE tool for urban railway bridges system tested and it operated as expected. Running on a web browser, the tool enables a user to consider and compare different maintenance strategies (e.g. preventive Maintenance or ‘Do-Minimum’), to guide the choice of the technical optimum solution according to the budget available.
Demo: Operational Asset Management in a Dutch environment
Discussion
Based in the Netherlands, Strukton Rail is a large European contractor in the field of performance-oriented railway maintenance. The Strukton Control Centre calls on a range of applied technologies (big data, IoT and machine learning) as part of a smart maintenance approach, converting condition data into predictive values and using this data to set up smart maintenance actions. This centre is an essential linking pin between monitoring the network and initiating the required interventions and organising the work to be done.
The Work Package sought to address three problems:
In response to these challenges, researchers developed and demonstrated prototypes of six modules:
All the prototypes were tested for asset monitoring and prediction (way-side, train-bound), decision support (operational planning), and their integration and validation.
Key findings
The added value of the tools was demonstrated in Strukton Rail’s maintenance areas. The six different modules are designed to be used separately or connected to existing or newly designed maintenance management platforms and applications, e.g. IRISsys (Erdmann), RamSys (Mermec), TIRIS (Thales) and Railigent (Siemens).
Use of asset data on a daily basis is very beneficial for maintenance. However, some specific ideas, e.g. using ABA data, turned out to be more complex than anticipated and thus merits more research in an operational environment.
Demo: Track Maintenance Decision Support Tool for a Swedish Heavy Haul Railway Line
Discussion
Today, the track maintenance planning process is assessed manually and requires significant human resources. A new tool, the Integrated Maintenance Decision Support Platform (IMDSP), aims to address this challenge. This data-driven platform brings together data acquisition, detection, prediction and optimisation of track geometry maintenance planning and scheduling, thus meeting the requirements of the Infrastructure Manager.
The IMDSP was demonstrated with a use case in northern Sweden, for the maintenance planning and scheduling of tamping actions on a freight track. The platform’s effectiveness was validated against three KPIs: corrective maintenance cost, number of corrective tamping actions (estimated), and track possession time.
Key findings
The IMDSP’s main added value lies in its ability to provide decision-makers with a wide range of alternative scenarios for planning and scheduling track geometry maintenance. This enables the infrastructure manager to quickly and effectively assess the long-term impact of strategic decisions and associated parameter adjustments. The platform also significantly increases the efficiency of managing the human resources allocated to this activity.
Although a computational process is used by the IMDSP to analyse and define the maintenance needs, this did not decrease the quality and feasibility of the planning generated by the tool.
The tool can reproduce the manual planning satisfactorily: 84% of correspondence in the work. Regarding the use of resources, the tool results only uses 16% of the resources that are necessary with today’s practices.
Demo: IAMS integration demonstrator “Gotham City”
Discussion
The “Gotham City” approach had two main objectives:
The “Gotham City” demo took into consideration the technical challenges of integrating heterogeneous IT systems, and well as the confidentiality of the shared data.
Key findings
The “Gotham City” HMI (Human Machine Interface) provides two main functionalities: 1) live monitoring: a platform user can observe the general status of the whole line (live interactive map and a dashboard for KPIs’ monitoring) and select specific assets if detailed investigation is needed; and 2) historical data visualisation: a platform user can select one of the map assets and access all the relevant information related to it.
Thanks to the design and implementation of the “Gotham City” demo, it is now clear that railway digitalisation will depend on:
The introduction of data-driven IAMS solutions requires trust in automated solutions; proper management of uncertainty (uncertainty aptitude), and reasoning about uncertain predictions/prescriptions.